What's Hot! | Products/ Tools | EFI Tuning | Basic Tuning | Advanced Tuning | Chassis Tuning | Advertise with us |
Exhaust Flow and Tuning
All Credit for this paper goes to:
Alvin Teo. We owe him a big thanks
This was my research project for my Physics of Modern Devices course which i took duringthe Spring semester of my Junior year in Rutgers. It was one of the electives i took for my minor in Physics. I got a 93% grade for this project, and the professor commented that my presentation could've been as detailed as this paper. You see, for my presentation, i just drew the whole system on the entire black board and then started briefly describing each component from the manifolds to the tailpipe, and not being very specific/technical. Oh well, at least i've passed the course right?
Introduction The engine is like an air pump; the more air that is allowed to flow through it, the more horsepower that you get out of it. In other words, if you have a free-flowing air intake and exhaust system in your average vehicle, you’ll get more horsepower because of the efficient flow of air into and out of the engine. Fuel requires air to burn and thus to produce energy. The more air that is available for combustion will also improve efficiency otherwise known as gas mileage.
The purpose of this project is to research on the present common air flow systems in today’s automobiles, particularly cars. This will be too general and cover too wide of a topic, as a car also uses air for various other mechanical purposes. So I will focus my project on the exhaust gas flow in a naturally aspirated fuel injected vehicles. Thus, I will not cover turbos, superchargers and nitrous oxide systems (which are forced inductions and are a substantial topic alone). And since some other students are doing projects on the engine itself, I will not spend too much time on how the air undergoes combustion in the engine. In short, my whole project will be divided into 4 sections:
1. The Basic Theory Behind the Relation Between Performance and Air Flow.
2. Analysis of the Exhaust System in an Average Car.
3. Methods on How to Improve Efficiency and Power.
4. Future Technological Trends and A Sneak Peak at "Electronic Mufflers".
Hopefully after the review of this project the reader will get a better understanding of how an exhaust system works in a vehicle and how power and efficiency can be unleashed with some modifications. This project is in no way suggestive for getting a car prepped for illegal street racing.
Relation Between Performance and Air Flow
Components that influence airflow into the engine are the:
1. air filter intake
2. air piping
3. mass air sensor (if applicable)
4. throttle body or carburetor
5. intake manifold
6. camshaft
7. intake port and valve of cylinder heads
8. turbo's compression, section, and supercharger (if applicable)
Components that influence airflow out of the engine are the:
1. exhaust valve and exhaust ports of the cylinder heads
2. camshafts
3. exhaust manifolds
4. turbo's turbine (if applicable)
5. exhaust tubing catalytic converters
6. muffler
When these components are modified to increase flow out of the engine, pumping losses are reduced. Pumping losses refer to the amount of horsepower (HP) used to push the exhaust gases out of the cylinders on the engine's exhaust stroke. Since less HP is used to get the exhaust out of the engine, more horsepower is available at the flywheel. An added benefit of reducing pumping losses is that fuel mileage will also increase.
No matter how much additional air is forced into the engine, no additional HP will be made unless additional fuel is also added. The energy that makes HP in an engine comes from the combustion of the fuel, not only the air. In general, every two HP produced requires one pound of fuel per hour. When modifications are performed that increase airflow into the engine, more air is available for the combustion of fuel. The combustion of the additional fuel is what translates into additional HP.
Air flow is not just influenced by the size (area) of the paths it takes into and out of the engine. It is also influenced by the speed at which it moves.
Specific Port Flow (cubic meter/sec) = Flow Velocity (m/s) x Average Path Area (m2)
Whenever an engine modification increases the average area of the airflow paths into and out of an engine, there is a chance the velocity of the flow will decrease. Most of the time the factor of velocity decrease is very small compared to the area increased, so flow is generally increased. If modifications are taken too far, the velocity will decrease more than the area increases, so flow is adversely affected (example - four inch exhaust system on a 1.6 liter engine).
In the following section, we will analyze the components of an exhaust system in a car and how air flows from the engine to the outside environment.
Analysis of the Exhaust System in an Average Car (Click Images for larger Photo)
The above is a diagram of the major components of an exhaust system in a car. Exhaust system components are designed for a specific engine. The pipe diameter, component length, catalytic converter size, muffler size, and exhaust manifold design are engineered to provide proper exhaust flow, silencing, and emission levels on a particular engine. In this section, I will go over the function and specifics of each component.
The Exhaust Manifold
The exhaust manifold is a pipe that conducts the exhaust gases from the combustion chambers to the exhaust pipe. Many exhaust manifolds are made from cast iron or nodular iron. Some are made from stainless steel or heavy-gauge steel. The exhaust manifold contains an exhaust port for each exhaust port in the cylinder head, and a flat machined surface on this manifold fits against a matching surface on the exhaust port area in the cylinder head.
Some exhaust manifolds have a gasket between the manifold and the cylinder head, as can be seen in the diagram below:
Exhaust manifold and gasket on an in-line engine
Gaskets are meant to prevent leakage of air/gases between the manifold and cylinder heads. The gaskets are usually made out of copper, asbestos-type material, or paper. In other applications, the machined surface fits directly against the matching surface on the cylinder head.The exhaust passages from each port in the manifold join into a common single passage before they reach the manifold flange. An exhaust pipe is connected to the exhaust manifold flange. On a V-type engine an exhaust manifold is bolted to each cylinder head.
The Exhaust Pipe (In-line)/ "Y" Pipe (V-type)
The exhaust pipe is connected from the exhaust manifold to the catalytic converter. On in-line engines the exhaust pipe is a single pipe, but on V-type engines the exhaust pipe is connected to each manifold flange, and these two pipes are connected into a single pipe under the rear of the engine. This single "Y" pipe is then attached to the catalytic converter. Exhaust pipes may be made from stainless steel or zinc-plated steel, and some exhaust pipes are double-walled. In some exhaust systems, an intermediate pipe is connected between the exhaust pipe and the catalytic converter. Some have a heavy tapered steel or steel composition sealing washer positioned between the exhaust pipe flange and the exhaust manifold flange. Other exhaust pipes have a tapered end that fits against a ball-shaped surface on the exhaust manifold flange. Bolts or studs and nuts retain the exhaust pipe to the exhaust manifold, as shown in the diagram below.
Some V-type engines have dual exhaust systems with separate exhaust pipes and exhaust systems connected to each exhaust manifold.
The Catalytic Converter
Three major automotive pollutants are carbon monoxide (CO), unburned hydrocarbons (HC), and oxides of nitrogen (NOx). When air and gasoline are mixed and burned in the combustion chambers, the by-products of combustion are carbon, carbon dioxide (CO2), CO, and water vapor. Gasoline is a hydrocarbon fuel containing hydrogen and carbon. Since the combustion process in the cylinders is never 100% complete, some unburned HC are left over in the exhaust. Some HC emissions occur from evaporative sources, such as gasoline tanks and carburetors.
Oxides of nitrogen (NOx) are caused by high cylinder temperature. Nitrogen and oxygen are both present in air. If the combustion chamber temperatures are above 1,371 degrees Celsius, some of the oxygen and nitrogen combine to form NOx. In the presence of sunlight, HC and NOx join to form smog.
Catalytic converters may be pellet-type or monolithic-type. A pellet-type converter contains a bed made from hundreds of small beads, and the exhaust gas passes over this bed (see Fig 1). In a monolithic-type converter, the exhaust gas passes through a honeycomb ceramic block (Fig 2). The converter beads, or ceramic block, are coated with a thin coating of platinum, palladium, or rhodium, and mounted in a stainless steel container. An oxidation catalyst changes HC and CO to CO2 and water vapor (H20). The oxidation catalyst may be referred to as a two-way catalytic converter (Fig 3).
Fig 1: Pellet-type catalytic converter
Fig 2: Monolithic-type catalytic converter
Fig 3: Oxidation catalyst changed HC and CO to CO2
Fig 4: Three-way catalytic converter operation
In a three-way catalytic converter, the converter is positioned in front of the oxidation catalyst. A three-way catalytic converter reduces NOx emissions as well as CO and HC. The three-way catalyst reduces NOx into nitrogen and oxygen (Fig 4).
Some catalytic converters contain a thermo-sensor that illuminates a light on the instrument panel if the converter begins to overheat. Unleaded gasoline must be used in engines with catalytic converters. If leaded gasoline is used, the lead in the gasoline coats the catalyst and makes it ineffective. Under this condition, tail pipe emissions become very high. An engine that is improperly tuned would also cause severe overheating of the catalytic converter. Examples of improper tuning would be a rich air-fuel mixture or cylinder misfiring.
Many catalytic converters have an air hose connected from the belt-driven air pump to the oxidation catalyst. This converter must have a supply of oxygen to operate efficiently. On some engines, a mini-catalytic converter is built into the exhaust manifold or bolted to the manifold flange.
The Resonator, Muffler, and Tailpipe
Since the resonator and muffler perform basically the same functions, I decided to write about them under one heading. Firstly, the main function of the muffler is to reduce the sound of the engine’s outcoming exhaust gases through the exhaust pipes to a minimal level. Since the muffler cannot reduce the noise of the engine by itself, some (if not most) exhaust systems also have a resonator between the catalytic converter and the muffler. Resonators are basically the second muffler, and are usually the "straight through" type.
The muffler quiets the noise of the exhaust by "muffling" the sound waves created by the opening and closing of the exhaust valves. When an exhaust valve opens, it discharges the burned gases at high pressures into the exhaust pipe, which is at low pressure. This type of action creates sound waves that travel through the flowing gas, moving much faster than the gas itself (up to 1400 mph = 625.8m/s), that the resonator and muffler must silence. It generally does this by converting the sound wave energy into heat by passing the exhaust gas and its accompanying wave pattern, through perforated tubes and tuning chambers. Passing into perforations and reflectors within the chamber forces the sound waves to dissipate their energy.
The above described and pictured muffler design is the most common type, the reverse-flow design, which changes the direction of exhaust flow inside the muffler. Exhaust gases are directed to the third chamber, forced forward to the first chamber, from where they travel the length of the muffler and are exhausted into the tailpipe.
Some mufflers are a straight through design in which the exhaust passes through a single perforated pipe into a outside chamber packed with metal, fiberglass, packed glass, or other sound absorbing (or insulating) material. As the exhaust gases expand from the perforated inner pipe into the outer chamber, they come in contact with the insulator and escape to the atmosphere under constant pressure. Because of this, the expanding chamber tends to equalize or spread the pressure peaks throughout the exhaust from each individual cylinder of the engine. This type of muffler is thus freer flowing and designed for the purpose of reducing back pressure and, consequently, makes slightly more noise.
The tail pipe basically carries the flow of exhaust from the muffler to the rear of the vehicle. Some vehicles have an integral resonator in the tail pipe. Like the resonator mentioned earlier, this resonator is similar to a small muffler, and it provides additional exhaust silencing. In some exhaust systems, the resonator is clamped into the tail pipe. Tail pipes have many different bends to fit around the chassis and driveline components. In general, all exhaust systems components must be positioned away from the chassis and driveline to prevent rattling. The tail pipe usually extends under the rear bumper, and the end of this pipe is cut at an angle to deflect the exhaust downward.
Methods on How to Improve Efficiency and Power
After the above discussion of the components in an automotive exhaust system, it is obvious that the principle of the engine as a pump is not being utilized to the fullest. Air is not allowed to flow too freely because of restrictions in the form of the catalytic converter, the resonator, and the muffler. However, these components are necessary by regulations to maintain safe exhaust gas emissions and minimal sound levels (noise suppression). Also, in part, it takes time and money to design an excellent performing and free flowing exhaust system; something that car manufacturers just can’t afford to waste resources on. This is where aftermarket companies come in to create cost effective options for performance minded car owners. Of course, a free flowing exhaust would be expected to make more noise than a normal one. But a good manufactured system has a deep throaty tone, while yielding increases in horse power and also passing emission tests. I will now go through some of the modifications of the exhaust system that would "unleash" some horsepower and efficiency, while still being street-legal.
Replacing the Exhaust Manifold with a Tuned Header
A header is a different type of manifold; it is made of separate equal-length cylindrical tubes with smooth curves in it for improving the flow of exhaust.
Each time a power stroke occurs and an exhaust valve opens, a positive pressure occurs in the exhaust manifold. A negative pressure occurs in the exhaust manifolds between the positive pressure pulses, especially at lower engine speeds. Some exhaust headers are tuned so the exhaust pulses enter the exhaust manifold between the exhaust pulses from other cylinders, preventing interference between the exhaust pulses. If the exhaust pressure pulses interfere with each other, the exhaust flow is slowed, causing a decrease in volumetric efficiency (and thus decrease in horsepower). Proper exhaust manifold/header tuning actually creates a vacuum, which helps to draw exhaust out of the cylinders and improve volumetric efficiency, resulting in an increase in horsepower.
Dual Exhaust Systems
For engines with the "V" type configurations, it would be more efficient to use a dual exhaust system than the "Y" pipe. In other words, two pipes (instead of one) connect the exhaust manifold/header to two catalytic converters, two resonators, and two mufflers. Thereby each manifold will have their own resonators, catalytic converters, exhaust pipes, mufflers, and tailpipes. The advantage of a dual exhaust system is that the engine exhausts air and gases more freely, thereby lowering the back pressure, which is inherent in an exhaust system. With a dual exhaust system, a sizable increase in engine horsepower can be obtained because the "breathing" capacity of the engine is improved, leaving less exhaust gases in the engine at the end of each exhaust stroke. This, in turn, leaves more room for an extra intake of the air-fuel mixture. The disadvantage of a dual exhaust system is that it would be costly due to the additional components. No doubt the addition of another exhaust system adds more weight to the car, but the increase in horsepower is substantial enough to outweigh the horsepower losses through additional weight.
Removing the Resonator
The resonator does not function also as emissions control device, so removing it and putting a straight pipe connecting the catalytic converter and the exhaust pipe will not cause the car to fail emissions test. Instead, some horsepower can be realized and not to mention the loudness of the exhaust. However, with a tuned muffler, the sound can be toned down to a deep throaty sound that is not irritable.
Upgrading to Larger Pipe Diameter
The factory exhaust pipes have diameters around 1.5" to 2" (some 2.25" for newer larger engine cars). Increasing the diameter of the piping will also increase the average path/cross-sectional area that the air can pass with a minute decrease in velocity. As mentioned before, if the diameter (and hence cross-sectional area) of the pipe is increased too much, the velocity of the air flow will decrease more than the area increases, so flow would be adversely affected and power would be lost.
So, depending on the size of the engine, the optimal size pipe to upgrade to varies from 2" to 2.5". On average, a naturally aspirated 2.5 liter engine would suffice with 2.25" exhaust piping from the catalytic converter back to the muffler inlet.
Mandrel Bent Versus Crush Bent Piping
Another way to upgrade the exhaust piping from the catalytic converter back to the muffler is to have the exhaust piping mandrel (heat) bent instead of the conventional crush bending. As the name suggests, mandrel bends are achieved through the heating of the piping before bending whereas crush bent just literally mean that the piping is bent entirely by force. However, the main difference between mandrel bent and crush bent piping is the ease of flow. Mandrel piping keeps the pipe at a constant cross-sectional area throughout a bend which makes exhaust flow easier. On the other hand, crush bending deforms the pipe at the bend(s), which can restrict the exhaust flow. The disadvantage of mandrel bending is that it is relatively expensive, because of the costs involved in operating a mandrel bending heat machine. A popular alternative is to get piping with larger diameter and then have it crush bent. This way, it kind of evens out the differences in air flow ease, especially if that particular exhaust pipe configuration has a lot of bends and 90 degree bends.
Straight Through Versus Reverse Flow Mufflers
Having a optimally free flowing exhaust all the way from the manifold would not do much good if the restrictive stock muffler is still used. The inlet and outlet diameters of the pipe in the muffler should also be as large as feasible, so as to allow free flow of exhaust gases. A straight through muffler would be preferred to a reverse flow muffler mainly because the process of air re-direction in the reverse flow muffler is too restrictive. A straight through muffler design would allow exhaust gases to be expedited out as efficiently as possible, although the muffling abilities would not be as efficient as that of the reverse flow design. Therefore it will be inevitable that the exhaust will sound louder than before, but as mentioned before a couple of times, an aftermarket straight through muffler uses noise suppressing material that tones down the sound to that of one that’s deep and throaty and not irritating. However, as will be discussed in the next section, a new generation of mufflers may be able to tackle this.
The Future
These days, you can’t think of exhaust system as just some crude plumbing hung on as an afterthought to pipe away air, heat, and to keep those decibels down. It’s become an integral part of the powertrain and under-car architecture critical to performance, fuel efficiency, and emissions reduction. There has already been development of low or zero emission vehicles already in the recent auto shows by major automobile manufacturers like Honda (Natural Gas vehicle) and Ford (Electric car). A oncoming development I would like to discuss about in this section is the Electronic Muffler.
As an executive with Walker, one of the major muffler makers involved in developing the concept puts it, "After the introduction of the catalytic converter in 1975, this is probably the most revolutionary technology that’s happened to exhaust systems in the entire history of the automobile."
While the idea is surprising, the basic principle isn’t hard to grasp. From a microphone and a crankshaft speed/position sensor, the computer receives input on the pattern of pressure waves (that’s what sound is, after all) the engine is emitting at its tail pipe. This data is processed using patented algorithms, which produce mirror-image pulses that are sent to speakers mounted near the exhaust outlet, creating contra-waves that cancel out the noise. In other words, the sensors trap the waveform signature of the engine, and the speakers generate anti-noise waves 180 degrees out of phase with the gas waves. This destructive interference idea is sort of like fighting fire with fire. The sound waves collide, wiping each other out. It doesn’t just mask the noise, it actually removes sound energy from the environment, and from the law of conservation of energy where the energy has to turn up someplace, all that is left is low-level heat.
Although electronic mufflers are not widely used (if ever) at present, they may be installed on vehicles in the near future. In 1989, a joint Electronic Muffler System development program was started and the University of Michigan’s Delphi study predicts that 20% of the cars produced in North America will have electronic mufflers by the turn of the century.
Well, if the electronic mufflers are really as effective as they claim to be and they were available now, we could build a perfect exhaust system using the setup described earlier with the addition of an electronic muffler then the problem of loud exhaust wouldn’t exist. But then again, by the time the electronic muffler is out in the market, technology might have other improvements of the exhaust system and we will again try to match components to produce more horsepower and attain better gas mileage (efficiency).
In conclusion, we go back to the basic analogy of the engine as a pump; the more air that can flow freely, the more horsepower that can be optimally achieved from the engine. This research paper has only dealt with how to get air OUT of the engine. It is important to note that the INFLOW of air also influences the output performance of the engine. As a matter of fact, we need the inflow of air before the outflow process starts. In brief, the inflow of air can be modified by removing the intake resonator, or even removing the entire airbox and installing a pipe with a cone-shaped filter at the end. There are many other ways to improve air inflow, but I shall not discuss about them as it would be outside he scope of this paper if I’m primarily interested in the outflow of exhaust gases.
Also, it is important to note that "horsepower" is a unit of energy over time. So the more energy it requires to do something, the less power you will get out of it. In other words, it is because motorcycles are lighter than cars that they can achieve similar if not higher horsepower. That is why race cars are stripped of the interior, air conditioning, and any other unnecessary weight. This way, there will be less weight to move, meaning less energy required and thus more power produced. That is why automotive engineers are trying to use materials of lighter weght, like plastics and carbon fiber.
Items to improve your exhaust flow can be found online at very competative prices. Check the following links and search for items for your car or truck:
***Remember*** to check for other relevant information in the columns and article tables.ATTENTION READER:
If you enjoyed the information and article you just read be sure to check out our newly released book with even more exciting photo's and information:How to Turbocharge and Tune your Engine
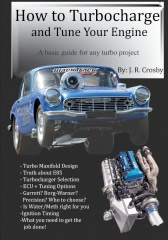
Want to know more about your particular Make and Model vehicle? All of these vehicles are covered in the tech, maintenance and repair articles found above. Enginebasics is the wiki or wikipedia of car part, repair, how to and tuning information. Let us be the class 101 for your automotive learning.
Ford | General Motors GM | Pontiac | Jaguar | Land Rover | Nissan |
Toyota | Honda | Lexus | Acura | Lotus | Scion |
Infinity | BMW | Mercedes | Mitsubishi | Ferrari | Maserati |
Lamborghini | Volks Wagen VW | Saab | Audi | Hyundai | Kia |
Subaru | Mazda | Chevy | Volvo | Caddilac | Dodge |
Chrylser | Daewoo | Porsche | Mercury | Freightliner | MG |
Individual Models
Ford Mustang | Mitsubishi Eclipse | Mitsubishi Evo | Subaru WRX / STI | Dodge Viper | Chevrolet Corvette |
Nissan Skyline | Honda S2000 | Nissan 350z | Toyota Supra | Chevy Camaro | Lotus Elise Exige |
Honda Civic | VW Golf | Dodge SRT-4 | Eagle Talon | Acura Integra | BMW M3 |
Nissan 240sx | Porsche 911 | Acura NSX | Honda Accord | Toyota Camry | Toyota MR2 |
VW R32 | Dodge Truck | Mazda Rx7 | VW Jetta | Sand Buggy | Nissan Sentra |
For the latest Automotive news and stories visit the websites below |
Our feature Build: An AWD V6 Civic